Energy Chain Cover for Clean-Room Medical Manufacturer
PROBLEM:
A medical manufacturer who had employed plastic energy chains on their production robots as a method of bundling their cables ran into issues with debris in their clean-room. Plastic energy chains have a tendency to rub and cause the introduction of debris inside and outside of the chain, which can be a big issue in manufacturing products for human contact and consumption.
REQUIREMENTS:
The customer needed an exterior cover for their energy chain that could withstand the repeated movement of their robot during operation, while at the same time keeping any debris from their energy chain contained within the jacket. The cover also needed to have low outgassing in order to meet the customer’s clean-room requirements and would need to be able to attach to the Igus style chain in order to maintain the same movements.
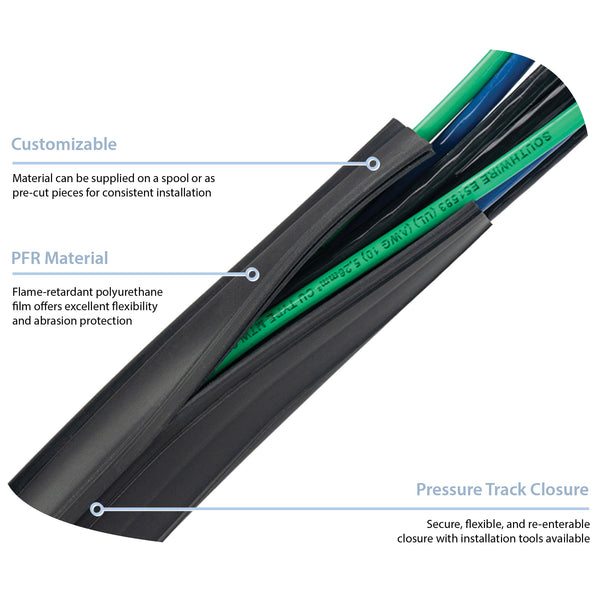
SOLUTION:
Zippertubing’s solution for this application is Zip-On® (PFR). Zip-On® (PFR) is abrasion resistant allowing it to withstand the repeated movement and pinching of the energy chain, will captivate debris with its secure Z-track closure, and has low outgassing due to it being entirely made of polyurethane. Zippertubing determined the correct length and method of attachment for each sleeve and provided them to the customer.
CONCLUSION:
Many companies that utilize energy chains are running into issues with debris being introduced into their systems by the chain links rubbing together. Zippertubing has a number of cable bundling products that can help with this issue whether they be used inside or outside of the energy chain system. Z-track products are especially effective as the secure closure prevents any debris from entering or exiting while the low profile of the track allows for it to avoid getting caught or pinched by the energy chain. While this customer used a round energy chain, many customers use rectangular energy chains, and Zippertubing is also able to build Zip-On® in custom rectangular shapes.